seeing the world in cubic feet
The method of describing the size of distribution centers may be changing, with footprint area no longer the key descriptor of size. In a late 2018 earnings call, Chief Financial Officer Brian Olsavsky said that Amazon could start using cubic feet, instead of square footage, to measure its fulfillment center footprint.[1] Amazon is not alone in thinking in terms of total facility volume. A recently completed O’Neal project represents the crossroads of high-volume, smaller footprint with high levels of automation and minimal staffing.
HP Hood is one of the country’s major dairy producers. Hood purchased a facility in Batavia, NY, and expanded production capacity, creating the need for an innovative warehouse solution to meet future requirements and to alleviate workforce availability issues. Hood’s desire was to use automation to store and pick orders. The resulting distribution center represents a next-step in facility automation, moving from a labor-based approach to a lights-out automated operation.
O’Neal partnered with an automation supplier to deliver a turnkey, refrigerated automated storage and retrieval system (ASRS) and case and layer-picking system. O’Neal and the automation supplier concepted the 25,000-pallet, nine-aisle storage system and incorporated a sophisticated means to automate the case and layer-picking process. Maintained at 35 degrees, automation removes the need for a constant labor force inside the temperature-controlled area.
Ryan White, O’Neal’s Manager of Manufacturing and Distribution Planning, worked with the automation supplier to develop the system. “This state of the art refrigerated Unit Load ASRS and Case Picking facility allows HP Hood to store, pick and ship orders with reduced labor and load trucks faster in a small footprint. The automated system does all the thinking and heavy lifting for HP Hood’s distribution operation so they can focus on producing a quality product for their customers.”
In addition to the automation system, O’Neal delivered design and construction of the 80,000 square foot building that includes a 55,000 square foot, 110-foot tall, rack supported structure for the ASRS system. In total volume, the high bay area provides over five million cubic feet of storage capacity.
White noted the savings and benefits derived from the approach used on the new facility. “The ASRS technology enables HP Hood to store 25,000 pallets in a building footprint of less than 55,000 square feet, which is three to four times less space required than a conventional building and, at the same time, get the benefits of automated pallet storage and picking.”
Incorporating a rack-supported structure with refrigeration, plumbing and other utilities required a high level of design and installation coordination. Additionally, floor flatness and levelness requirements become even more critical to support ASRS systems that are picking pallets at elevations as high as 100 feet.
The remaining 30,000 square feet provides a shipping area which is fed both by the ASRS and from the existing warehouse to which the new structure is tied.
O’Neal is also supporting HP Hood as its representative during prestart-up, start-up, and performance testing activities of the automated system. The O’Neal team is working at the direction of HP Hood and System Logistics, the automated system supplier, to coordinate the testing activities and provide regular interval reports to ensure transparency of these testing activities.
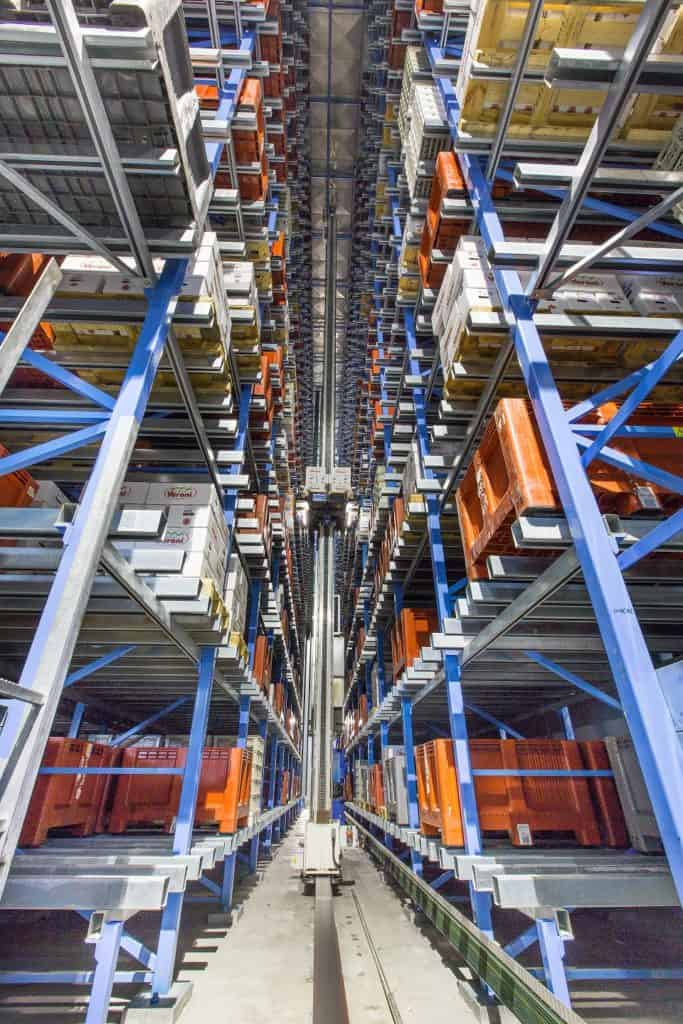
get connected